Wind tightness in every corner
Surface wind tightness is realised using high quality roof membranes. Nowadays, diffusive membranes are increasingly being used. Although these products are vapour-permeable they are still waterproof and windtight. This apparent contradiction can be explained if we look at how monolithic membranes work. Monolithic films allow the molecular transportation of vapour but, thanks to a waterproof layer, they prevent any penetration by wind or rain.
With its three products Ampatop Protecta, Ampatop Secura and Ampatop Seal Ampack offers three roof membranes with this ground-breaking monolithic technology.
Surface installation
Roof membranes also have the same function as the windtight layer. They are generally positioned on the cold side of the construction. If they are fastened as tension-free and with as few creases as possible, suction and load effects on the areas of adhesion and connection can be avoided. This helps to avoid the splitting of the membrane at clip points and / or rupturing at the edge connections. The lowest membrane is introduced via the inlet sheet and the highest membrane is pulled over the ridge. Adhesive strips, liquid adhesives and other adhesives ensure the wind tightness but do not act as a mechanical safeguard. Dirt, dust and ice on the surface of the membranes can radically reduce the adhesion of even the best adhesives.
In order to ensure that the membranes are completely wind-proof, they must be bonded as soon as they have been placed in the area of overlap. The end laps must be bonded as well to ensure wind tightness. Ideally the overlaps are bonded from the centre of the roof towards the edges, in order to minimise the risk of creases.
Planning – the A and O
Good planning is essential for the successful construction of a perfect roof. The challenges to be overcome differ depending on the shape of the roof and the construction required. A roof in a mountainous region is clearly subject to greater stress than a roof in a flat area. It is therefore sensible to ensure that the construction method, the location and the needs of the building contractor have been aligned.
Seals in detail
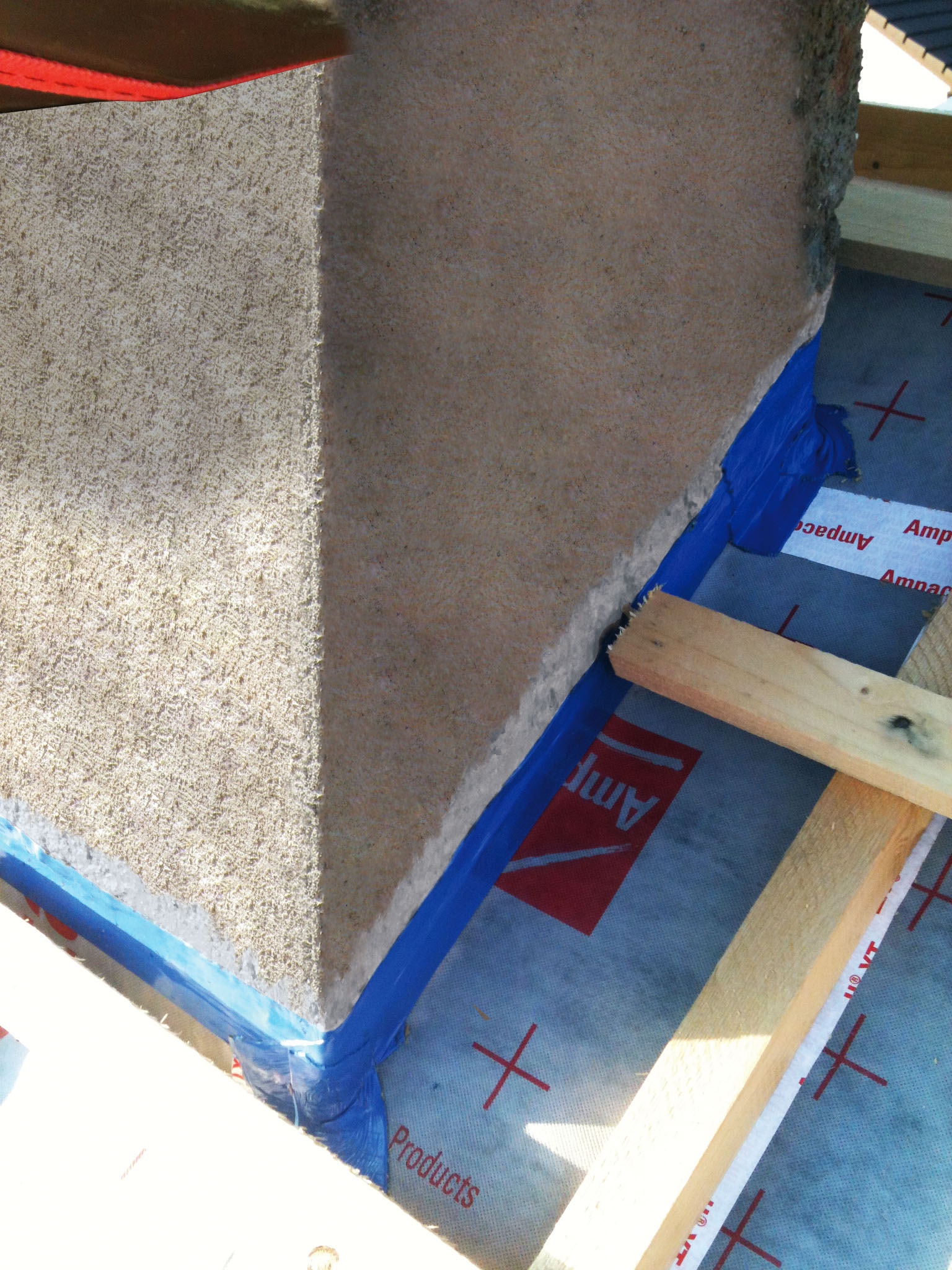
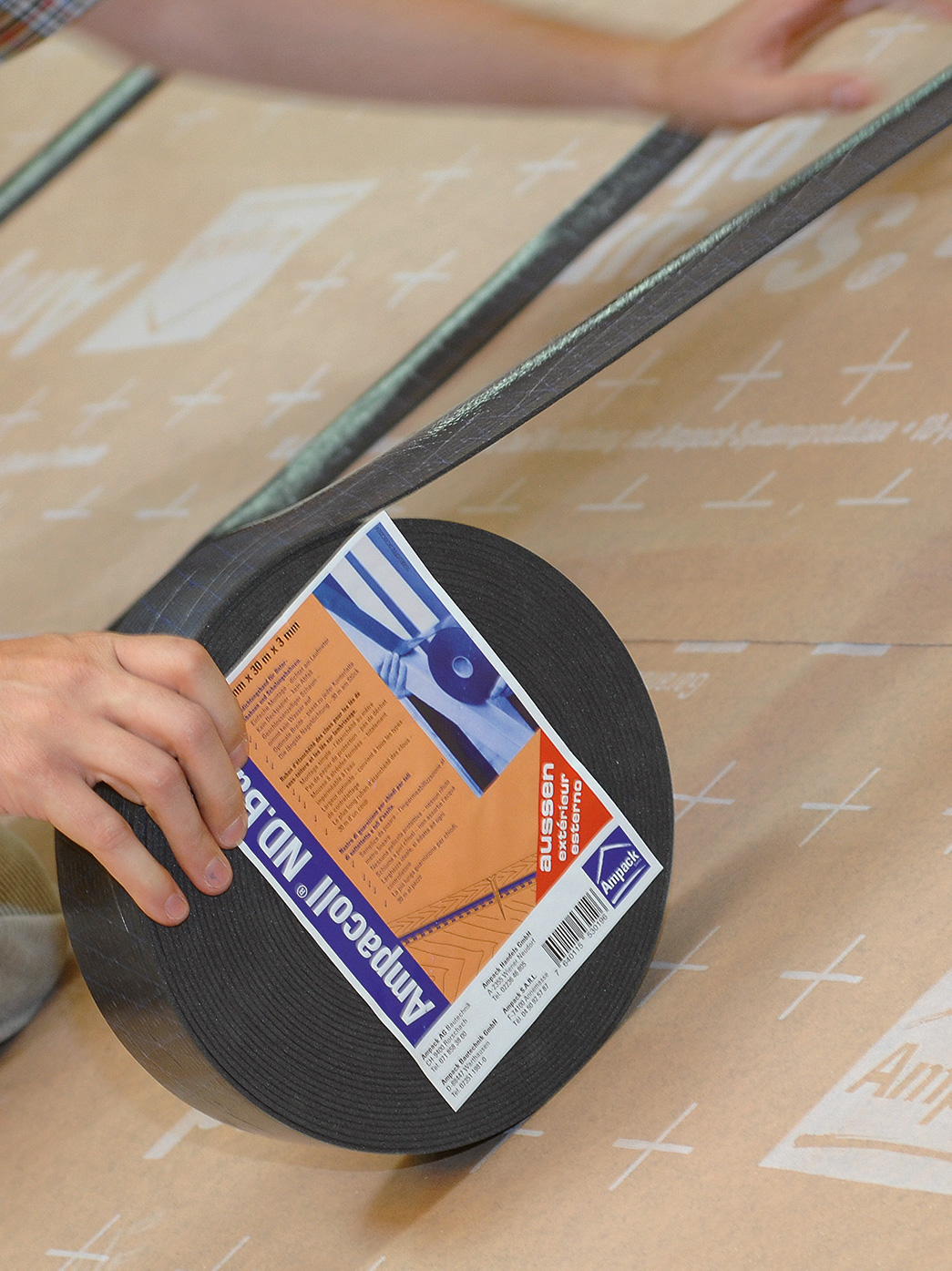
The following details in particular must be observed when creating the windtight layer:
- Nail and screw positioning in the counter battening must be sealed with nail sealing pads and / or band, e.g. with Ampacoll ND.Band.
- Edges to chimneys, roof windows and other installations must be built out and sealed to the height of 15 cm at least, e.g. with Ampacoll Superfix.
- Connections to inflow sheets must be sealed, e.g. with Ampacoll Superfix.
- Penetrations such as outlet vents, chimneys, etc. must also be sealed to make them rainproof and windtight, e.g. with Ampacoll BK 535.
Roof windows and other surface penetrations are fitted using strips of the roofing membrane to ensure that they are rainproof and windtight. You will find the recommended combination of materials in our adhesives matrix.
Preparation of unsuitable surfaces
Facing-side water penetration
Pull up the membranes on the plank!
Rough surfaces
Clean surfaces so that the membranes are not damaged.
Pollution
Avoid pollution with chemical liquids.
Avoid creases
Lay the vapour retardant avoiding bulges and creases. However, make sure that there is room for expansion.
Windtight penetrations and connections
Penetrations and connections must also be windtight.
Water drainage
This must not be blocked. No chips or sawdust on the membrane!
Dirt, dust and ice
Materials, connections and surfaces to be bonded must be cleaned if necessary to ensure that they are clean, dry, and dust, grease and ice free.
Power and loadfree connections
Ensure the correct execution of power and loadfree connections.
Securing using counter battening
Do not leave the construction site until all the membranes have been secured with counter battening.
Hard base
In critical areas ensure that a hard base is provided.
Attaching wind seals
Attach the membranes to the underlying construction in the overlap area using staples. Be certain to use them liberally!